The quality of finished pellet feed is the basis for the healthy development of the feed industry and is directly related to the production efficiency of the breeding industry, user interests and the reputation of the feed factory. At the same time, the stability of feed products is also an important guarantee for the development of the feed industry and animal husbandry. However, in the production of pellet feed, there is often a problem that there is a certain difference between the quality of the finished product and the formula design.
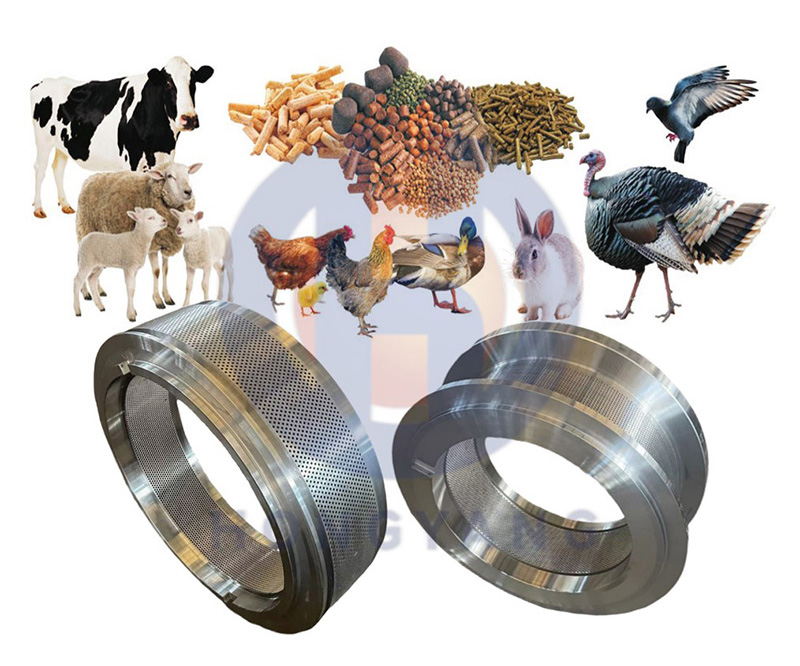
To this end, factors affecting the quality of finished pellet feed products should first be analyzed, and then effective solutions should be found.
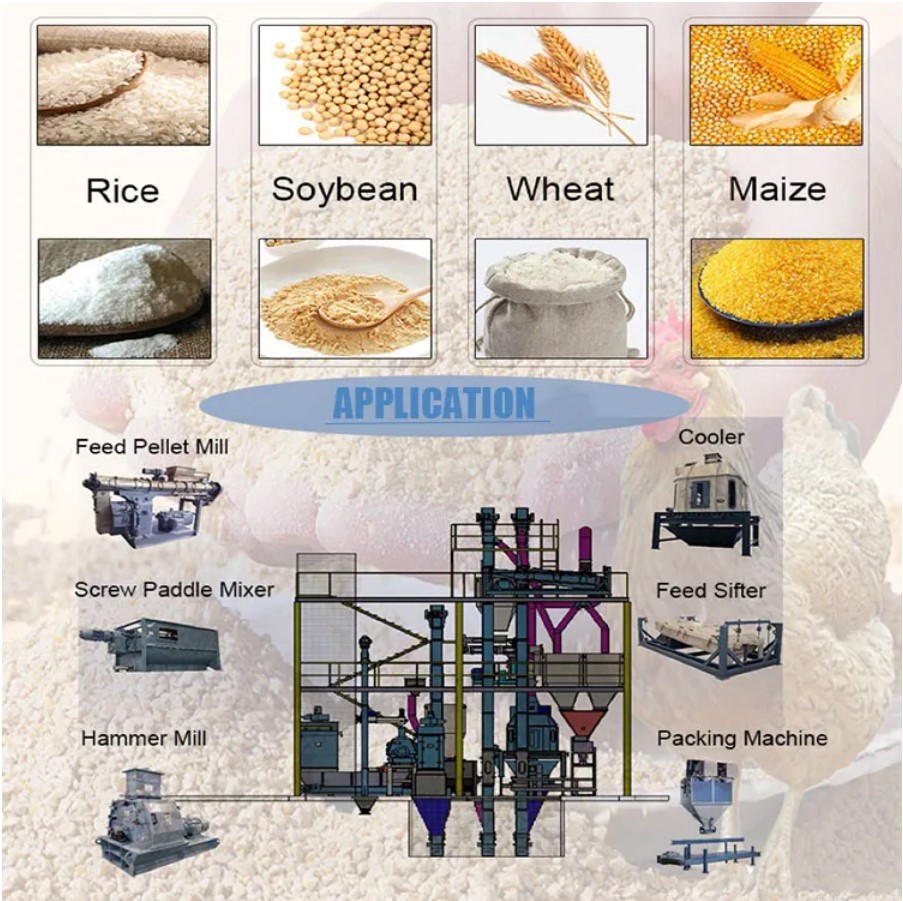
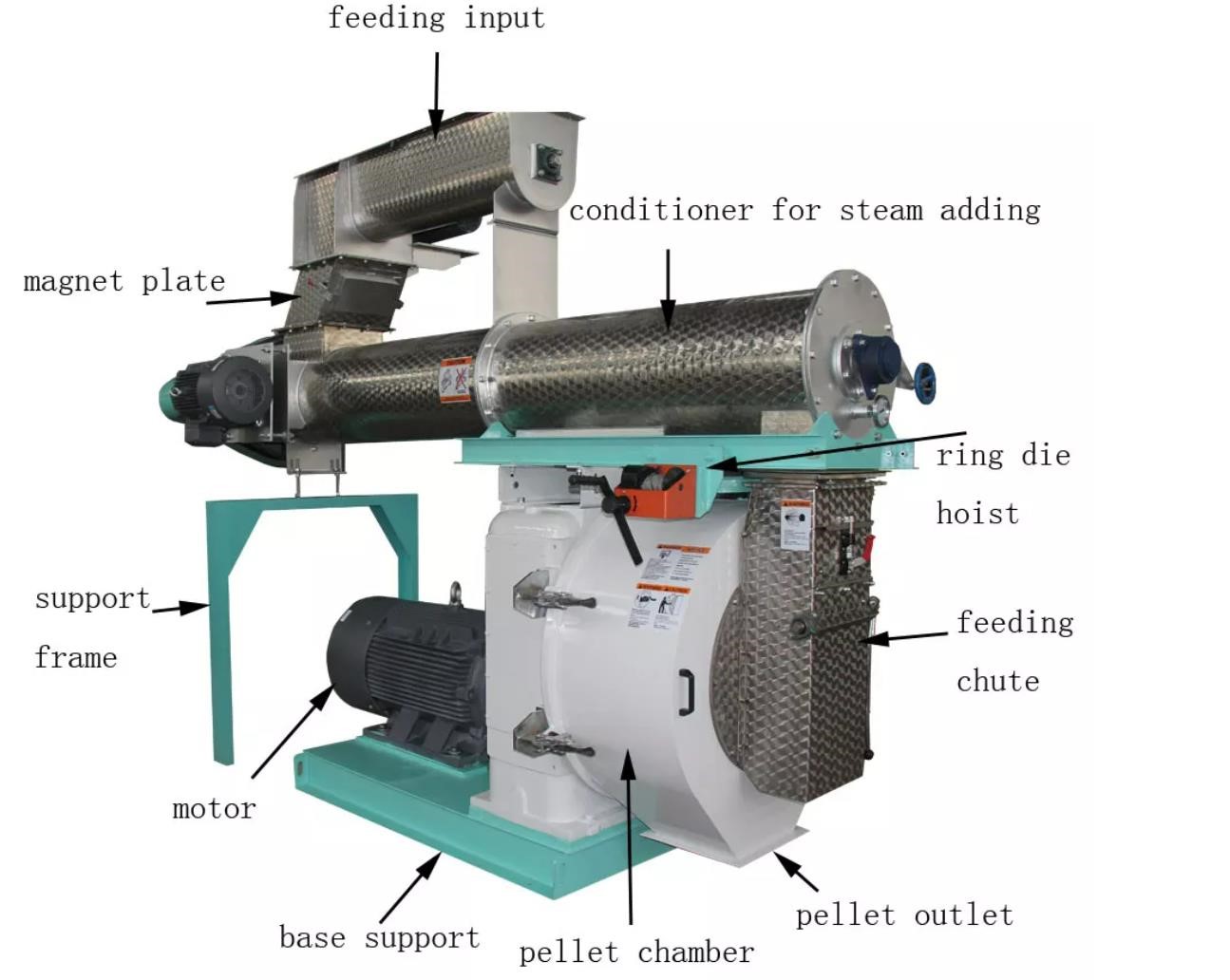
1. Influence of the quality of feed raw materials: Raw materials are the basis for the quality of finished feed products. The raw materials for feed mills come from all directions. Even if they are the same raw materials, due to the origin, variety, soil, harvesting method and maturity at harvest, processing method, climate conditions, Depending on the moisture content, degree of mildew, etc., the nutrient content also varies greatly. Especially in the season when feed raw materials are in short supply, the varieties are more diverse, the quality is worse, and adulteration is serious. In this case, it is necessary to pay attention to raw material analysis, accumulate and organize commonly used raw material data, conduct finished product inspection, and find out the differences and regularities of raw materials. In addition, the storage time of raw materials will also affect their nutritional value, among which the problem of additive premixes is more prominent. If the additive has poor stability, it will quickly fail under the influence of ultraviolet rays and oxidation. Vitamins are easy to oxidize, and sulfates are easy to absorb moisture and return moisture.
2. Ingredients affect the accuracy of the ingredients, which directly affects the quality of the finished product. When designing formulas, the accuracy generally reaches two decimal places, but in actual production it does not reach this level. The batching measurement equipment in the feed factory is the key to the accurate realization of formula design. When computer-controlled batching is used, whether the advance design of various raw material ingredients is reasonable or not is the key to the accuracy of batching.
3. The influence of mixing uniformity: Mixing uniformity is an important quality indicator. It means whether the actual composition of the product or even each portion of the diet consumed by livestock and poultry is consistent with the formula design. Among them, the physical properties of premixes vary greatly due to trace components, and the addition amount of some components is very small, making it even more difficult to ensure uniform distribution. The factors that affect mixing uniformity mainly include the following three aspects:
3.1 Equipment: Poor equipment, poor performance or worn mixing equipment will affect the mixing uniformity.
3.2 Physical properties of powder particles. Modern compound feed is a product containing many different ingredients. Many ingredients vary greatly in particle size, shape, specific gravity and addition level, which all affect the mixing uniformity.
3.3 Operating conditions: including the mixing ratio of each component in the mixed material, loading coefficient (the mixing amount exceeding the design amount will seriously affect the mixing uniformity), feeding method, feeding sequence, feeding speed, mixer speed and mixing time, etc. are all important for uniform mixing. have an impact.
Post time: Jan-19-2024