In pellet feed processing, high pulverization rate not only affects feed quality, but also increases processing costs. Through sampling inspection, the pulverization rate of feed can be visually observed, but it is not possible to understand the reasons for pulverization in each process. Therefore, it is recommended that feed manufacturers strengthen effective monitoring of each section and implement prevention and control measures simultaneously.
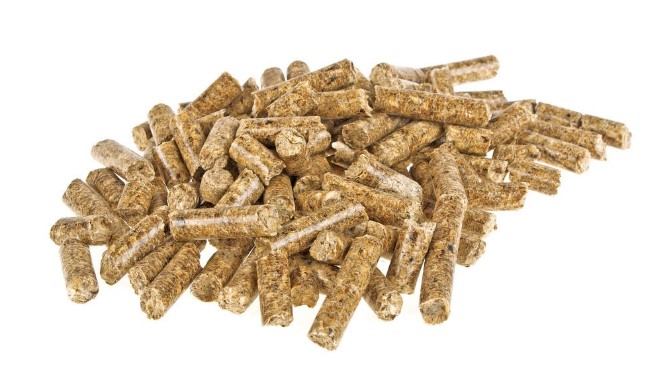
1、 Feed formula
Due to differences in feed formulations, the processing difficulty may vary. For example, feed with low crude protein and fat content is easier to granulate and process, while feed with high content is less likely to form, resulting in loose particles and a higher pulverization rate. So when considering feed granulation comprehensively, the formula is the prerequisite, and the difficulty of processing should be considered as much as possible to ensure the overall quality.As a customer of Hongyang Feed Machinery, we can provide you with professional feed formulas to increase your production capacity and improve the quality of feed.
2、Crushing section
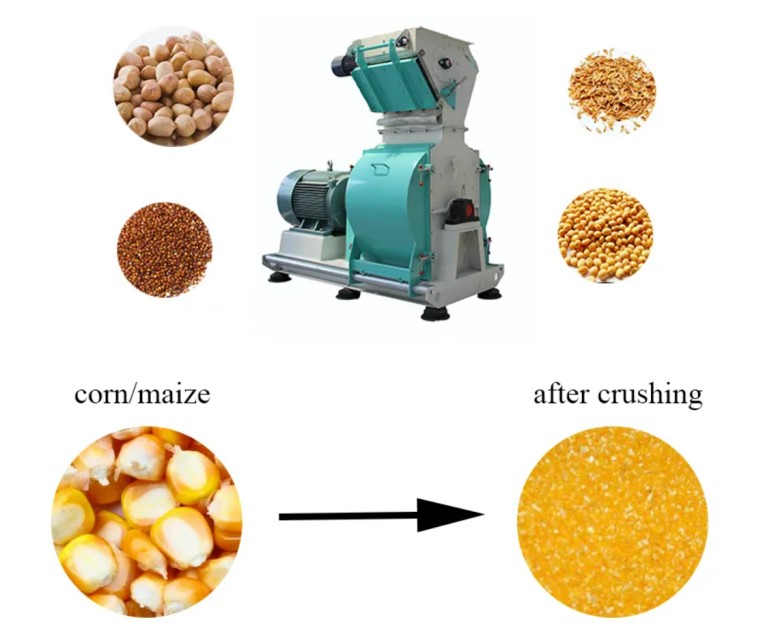
The smaller the particle size of raw material crushing, the larger the surface area of the material, the better the adhesion during granulation, and the higher the granulation quality. But if it is too small, it will directly destroy the nutrients. Choosing different material crushing particle sizes based on comprehensive quality requirements and cost control is crucial. Suggestion: Before pelletizing livestock and poultry feed, the particle size of the powder should be at least 16 mesh, and before pelletizing aquatic feed, the particle size of the powder should be at least 40 mesh.
3、Granulation section
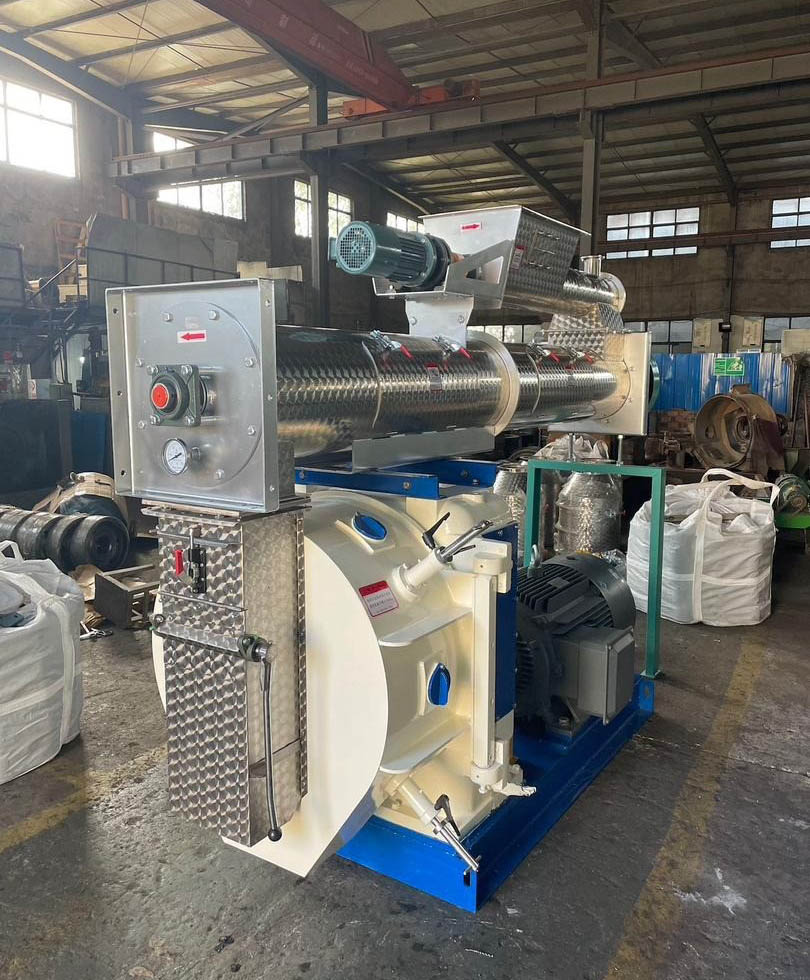
Low or high water content, low or high tempering temperature all have a significant impact on the granulation quality, especially if they are too low, they will make the granulation of feed particles not tight, and the particle damage rate and pulverization rate will increase. Suggestion: Control the water content during tempering between 15-17%. Temperature: 70-90 ℃ (the inlet steam should be depressurized to 220-500kpa, and the inlet steam temperature should be controlled around 115-125 ℃).
4、 Cooling section
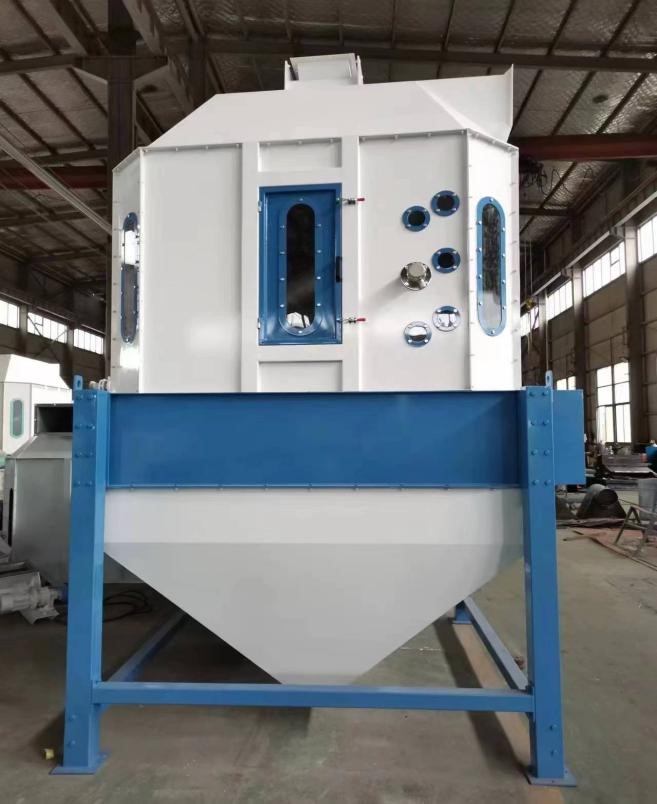
Uneven cooling of materials or excessive cooling time can cause particle bursting, resulting in irregular and easily fractured feed surfaces, thereby increasing the pulverization rate. So it is necessary to choose reliable cooling equipment and evenly cool the particles.
5、 Screening section
Excessive thickness or uneven distribution of the grading screen material layer can lead to incomplete screening, resulting in an increase in powder content in the finished product. The rapid discharge of the cooler can easily cause excessive thickness of the grading sieve layer, and attention should be paid to preventing it.
6、 Packaging section
The finished product packaging process should be carried out in a continuous production process, with the finished product warehouse storing at least 1/3 of the finished product before starting packaging, in order to avoid the increase of powder in the finished product caused by the feed falling from a high place.
Post time: Oct-24-2023