The reasons for cracking of ring molds are relatively complex and should be analyzed in detail; however, they can be summarized into the following reasons:
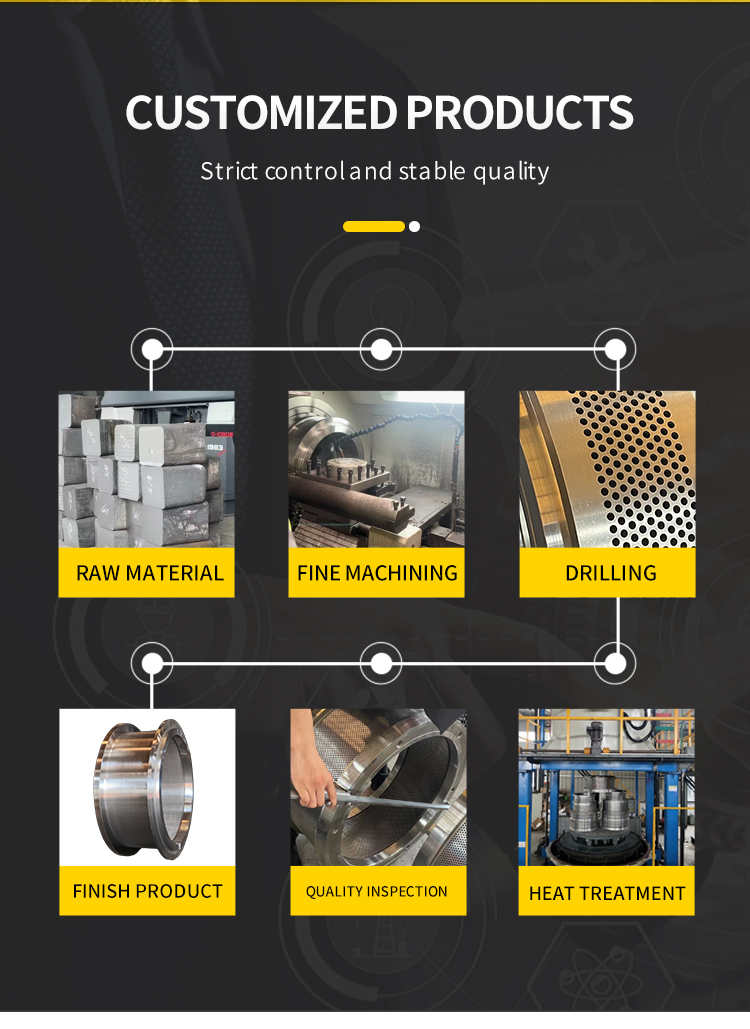
1. Caused by ring die material and blank quality
1) The material used in the ring die is one of the important reasons. At present, Chinese ring dies mainly use 4Cr13 and 20CrMnTid, which are relatively stable. However, there are different manufacturers of materials. For the same material, there will be certain differences in trace elements, which will affect the quality of the ring mold.
2) forging process. This is an important link in the mold manufacturing process. For high-alloy tool steel molds, there are usually requirements for the metallographic structure such as carbide distribution in the material. The forging temperature range should also be strictly controlled, correct heating specifications should be formulated, correct forging methods should be adopted, and slow cooling or timely annealing after forging should be performed. Irregular processes can easily lead to cracks in the ring die body.
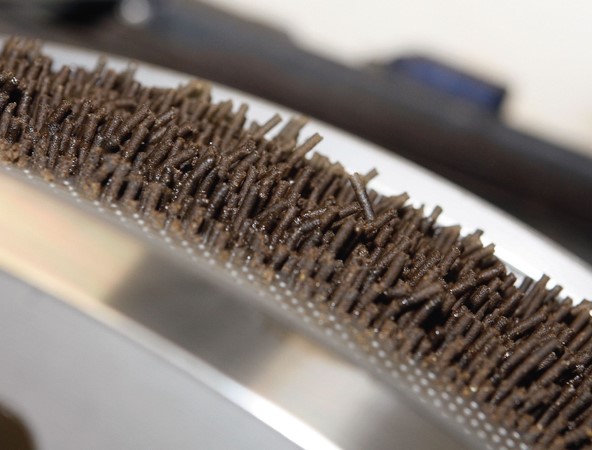
3) Preparation for heat treatment. Depending on the material and requirements of the mold, preparatory heat treatment processes such as annealing and quenching and tempering are used to improve the structure, eliminate structural defects in forging and blanks, and improve processability. Appropriate preparatory heat treatment of high carbon alloy mold steel can eliminate network carbides, spheroidize and refine the carbides, and promote uniform carbide distribution. This will help ensure the quality of quenching and tempering and increase the life of the mold.
2. Ring die heat treatment
1) quenching and tempering. This is a key link in mold heat treatment. If overheating occurs during quenching and heating, it will not only cause greater brittleness of the workpiece, but also easily cause deformation and cracking during cooling, seriously affecting the life of the mold. The heat treatment process specifications should be strictly controlled and vacuum heat treatment should be used. Tempering should be carried out in time after quenching, and different tempering processes should be adopted according to technical requirements.
2) stress relief annealing. The mold should be subjected to stress relief annealing after rough machining to eliminate the internal stress caused by rough machining to avoid excessive deformation or cracks caused by quenching. For molds with high precision requirements, stress relief tempering treatment is required after grinding, which is beneficial to stabilizing the accuracy of the mold and increasing its service life.
3. Opening ratio of ring mold
1) If the opening rate of the ring die is too high, the possibility of ring die cracking will increase. Each ring mold manufacturer will have relatively large differences due to different heat treatment levels and processes. Generally, our company's products can increase the opening rate by 2-6% on the basis of domestic first-class brand molds, and can ensure the service life of the ring mold.
4. Ring die wear
1) When the ring die is worn to a certain thickness and the strength is reduced to the point where it cannot withstand the pressure of granulation, cracking will occur. It is recommended that the ring die be replaced in time when the ring die is worn to the point where the pressure roller grooves are flush.
5. Use of ring die
1) During the granulation process of the ring die, the amount of material entering cannot be allowed to operate at 100% load because of the high granulation output of the ring die itself. Such long-term and high-intensity operation will also lead to cracking of the ring die. . We recommend controlling the load at 75-85% to ensure the service life of the ring die.
2) If the ring die and pressure roller are pressed too tightly, cracking may easily occur. Generally, we require that the distance between the ring die and the pressure roller should be controlled between 0.1-0.4mm.
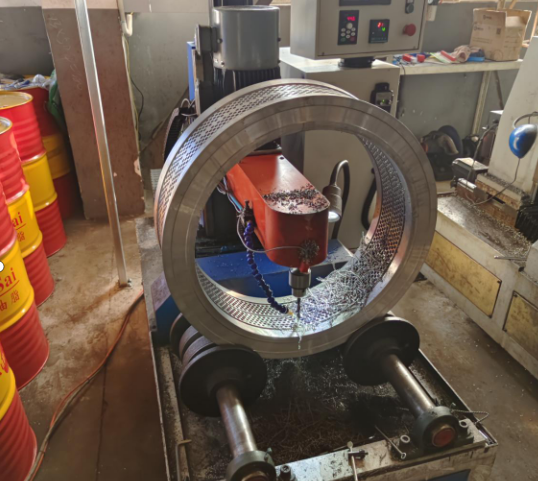
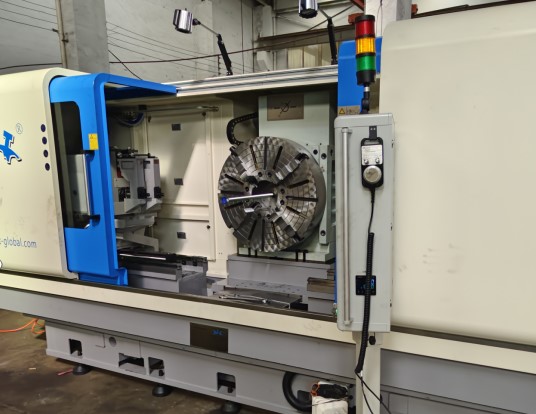
6. Sundries
1) Cracking is more likely to occur when hard objects such as iron blocks appear in the granulated materials.
7. Ring die installation and granulator issues
1) The ring die is not installed tightly and there is a gap between it and the granulator. The ring die may also crack during the granulation process.
2) After heat treatment, the ring mold will be greatly deformed. If not repaired, the ring mold will crack during use.
3) When the granulator itself is defective, such as the main shaft of the granulator shaking, etc.
Technical Support Contact Information:
Whatsapp: +8618912316448
E-mail:hongyangringdie@outlook.com
Post time: Jan-25-2024